Product
CBN Core Line
Product
CBN Core Line
Various lineup optimize a long time machining on hardened steel
Various lineup optimize a long time machining on hardened steel
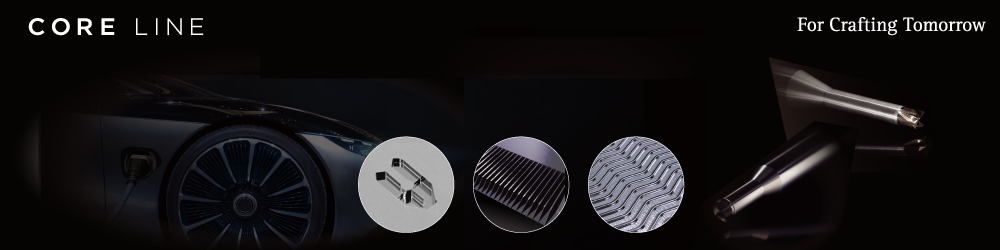
What is CBN Sintered Alloy?
CBN(Cubic Boron Nitride) sintered alloy is 3 times harder than Tungsten carbide, second hardest material next to diamond. Moreover strong heat-resistant and high thermal conductivity. However less tough characteristic of CBN often causes chipping of tool edge easily. Accordingly, CBN is recommended for finishing of hard materials with less cutting load on the tool edge, which guarantees extra long tool life.
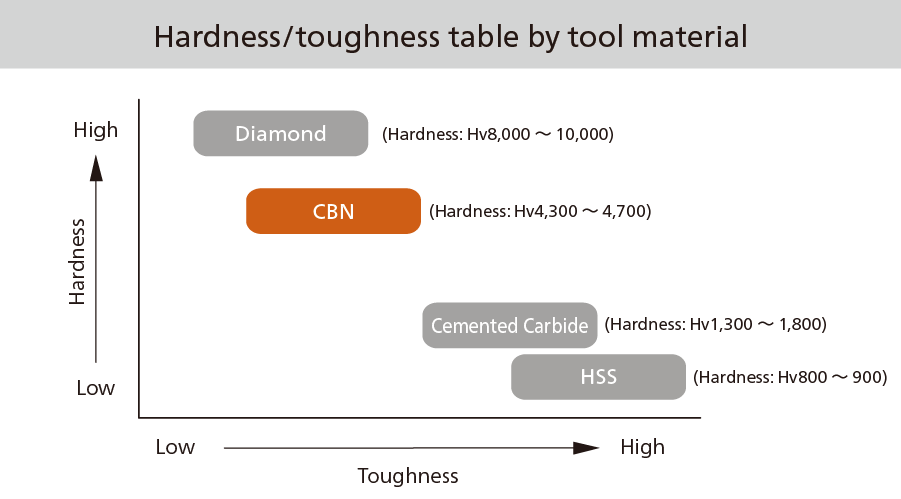
Leaflet
CBN trial kit
For users using CBN for the first time
CBN trial kit Comes in a package tool, work and NC data. This product allows you to conduct machining tests focusing on using CBN end mills for finishing machining. Furthermore, our engineer analyzes machining result, and support customer precision micro machining.
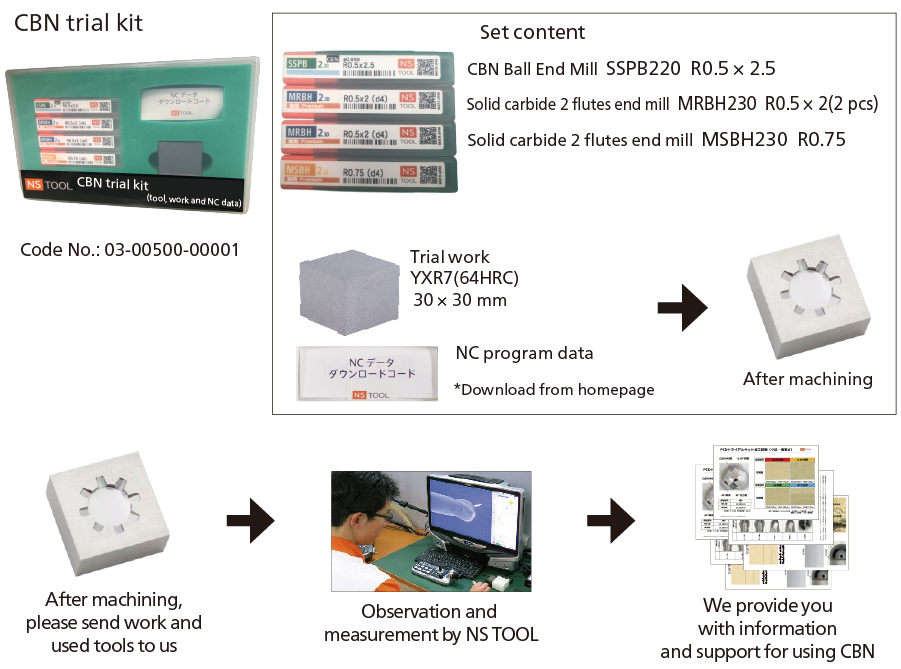
Measurement details
We analyze and report on the tools and workpieces after machining from the following perspectives.
Tool observation
Work condition
Download NC data
You can download CBN trial kit NC program from following link.
*To download, there should have a
download code that comes with the trial kit.
Download