Products
Features of NS TOOL End Mills
Excellent Cutting Edge
Sharpened cutting edge realizes excellent surface even if cutting depth of 0.01mm in finish cutting.
One example, drop off of sintered carbide grain is hardly observed at cutting edge of NS TOOL End Mill as shown in below pictures.
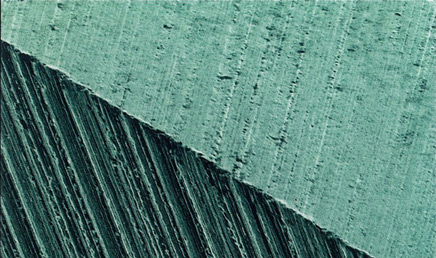
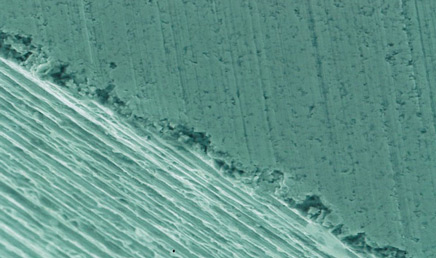
MACH225 Ball End Mill for high speed cutting of hardened steels
MACH225 is designed for direct carving with high-speed cutting for hardened steel (over 60HRC). In traditional type of ball end mills, cutting resistance and mechanical shock is big due to its negative rake angle. On the other hand, MACH225 reduces such negative effect by employing sharp & positive rake angle which finally leads to long tool life and bigger depth of cutting.
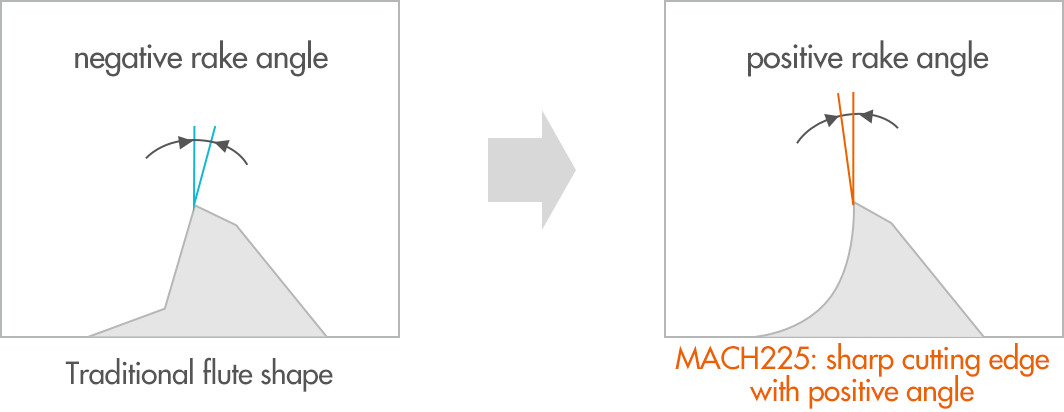
Comparison of cutting time
Comparison of cutting time (Rough cutting by recommended milling condition of each company.)
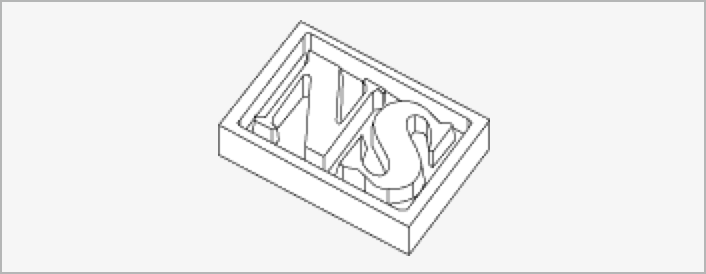
Work Material: SKD11 60HRC
Size: 80mm ? 44mm ? 4mm
Spindle Speed [min-1] | Feed [mm/min] | Depth of Cut (ap x ae) [mm] | |
---|---|---|---|
MACH225 1R | 20,000 | 2,000 | 0.2 x 0.5 |
Rival A 1R | 16,000 | 800 | 0.06 x 0.6 |
Rival B 1R | 28,500 | 2,600 | 0.04 x 0.1 |
MHD445・645 Square End Mill for hardened steel
Generally cutting edge of end mills for hardened steel is designed with negative lake angle in order to increase chipping resistance. However it effects on cutting accuracy and tool life in worse due to dull cutting edge.
MHD445・645 brought dramatic improvements in cutting accuracy and tool life by employing special design of cutting edge and high-grade of super-micro grain carbide with higher chipping resistance.
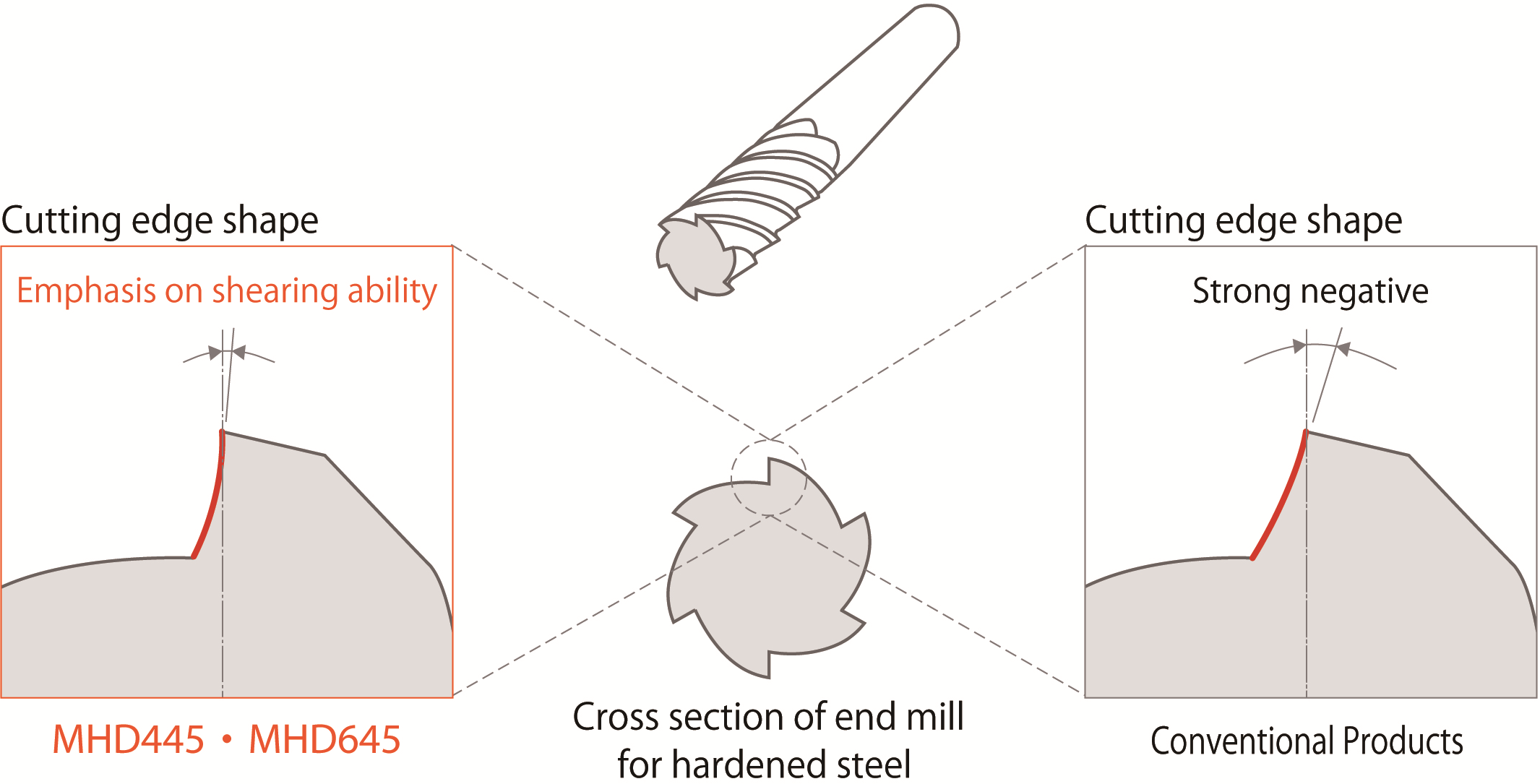
Comparison of Tool Life
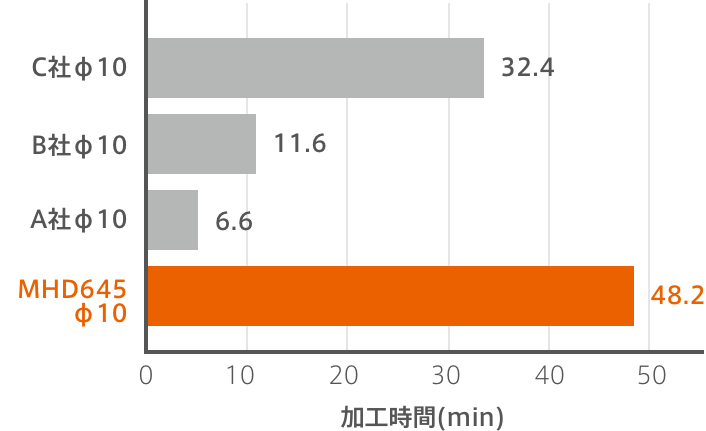
Work Material: SKD11 60HRC
Cutting Condition:
・Spindle Speed: 3,200 min-1
・Feed: 1,000 mm/min
・Depth of Cut(ae x ap): 0.1 mm x 15 mm
・Air blow